"THE X FACTOR ARE OUR PEOPLE, WHO HAVE YEARS OF EXPERIENCE HOW TO MAKE THE MOST COMPLEX DIES OF THE WORLD"
RAMON BRAUER ABOUT 2019 AND THE OUTLOOK FOR 2020
Ramon, you have been at Adex for 1 year now in the role of managing director. In this year a lot happened with the global economics that impacted the extrusion world. However, a change seems to be coming. What do you think about the current situation the market is in?
The global aluminium extrusion market is still growing. The increase in the construction of ‘green buildings’ is one of the key factors driving the growth in this market. Aluminium is becoming a mainstream material that has now been adopted by the constructors in the building industry. The automotive sector is in a transition from the internal combustion engine to the hybrid or full electric cars. I expect that 2020 will be a key year in this transition. On this moment the number of automotive projects we are in is less than the years before but I expect that this could turn around in the coming months. Global automotive players have been investing too much into the electric cars to not continue the road that they have gone into.
One topic that is becoming a hotter is sustainability in the aluminum extrusion industry. What role can a toolmaker play in the sustainability or better said, what is Adex doing on sustainability?
Sustainability is certainly important for the next coming years. Especially in the manufacturing industry. Thinking green is the phrase that is repetitively used in every new project. The shift to aluminium will therefore be important for every business. ‘Green buildings’ are environment-friendly, energy-efficient and have low carbon-emissions, being the reason the be constructed across the globe. Also the automotive and transport sector have a focus on saving weight. Extruded aluminum is used in the fabrication of various aluminum-made parts.(Battery holders, bumpers, etc.) Adex is already working on sustainability. By co-engineering with our customers, we can customize a construction or profile. Putting a much as technology into a profile as possible. In this way preventing unnecessary tools to be made. By simulating, we can save our customers a trial pressing, but this can also save scrap by shortening the transversal seam in the profile (billet to billet) Due to our technologies we are improving the lifespan of the dies a much as possible. So basically pushing out more kilogram per tool before it needs to be replaced. This to reduce our customers consumption of dies saving steel and energy.
What is de current focus of Adex and how will this be achieved?
Our motto for 2020 is “First Time Right”. For Adex this means that we're going to look closely at ourselves what we are not doing right the first time in our production. We need to analyze whether this lies in our processes, people or procedures. If we can improve this by training our people, automating our processes and transferring our knowhow to the entire factory this will result in better dies and shorter delivery time for our customer.
What is the ‘X-factor’ Adex has in the market?
Adex is known in the market for its special Dies (Technology Die) in the range of 79mm up to 1000mm. The X factor are our people, who have years of experience how to make the most complex dies of the world. They never stop looking at new ideas or new ways to get the job done making sure that the customers gets the best tool for the job.
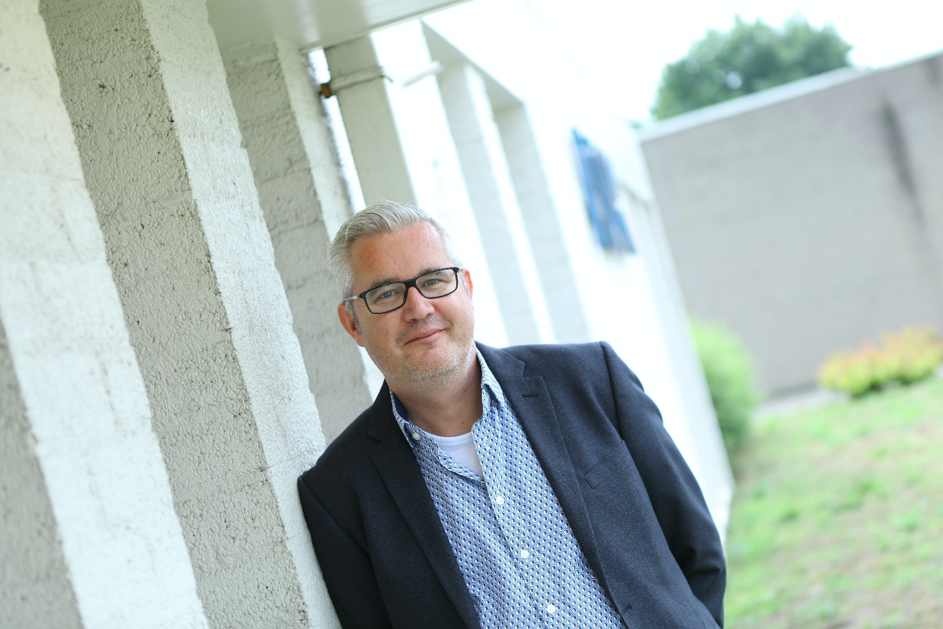
Ramon Brauer
Managing Director Adex.